P for Soft-Paste Porcelain
Published on
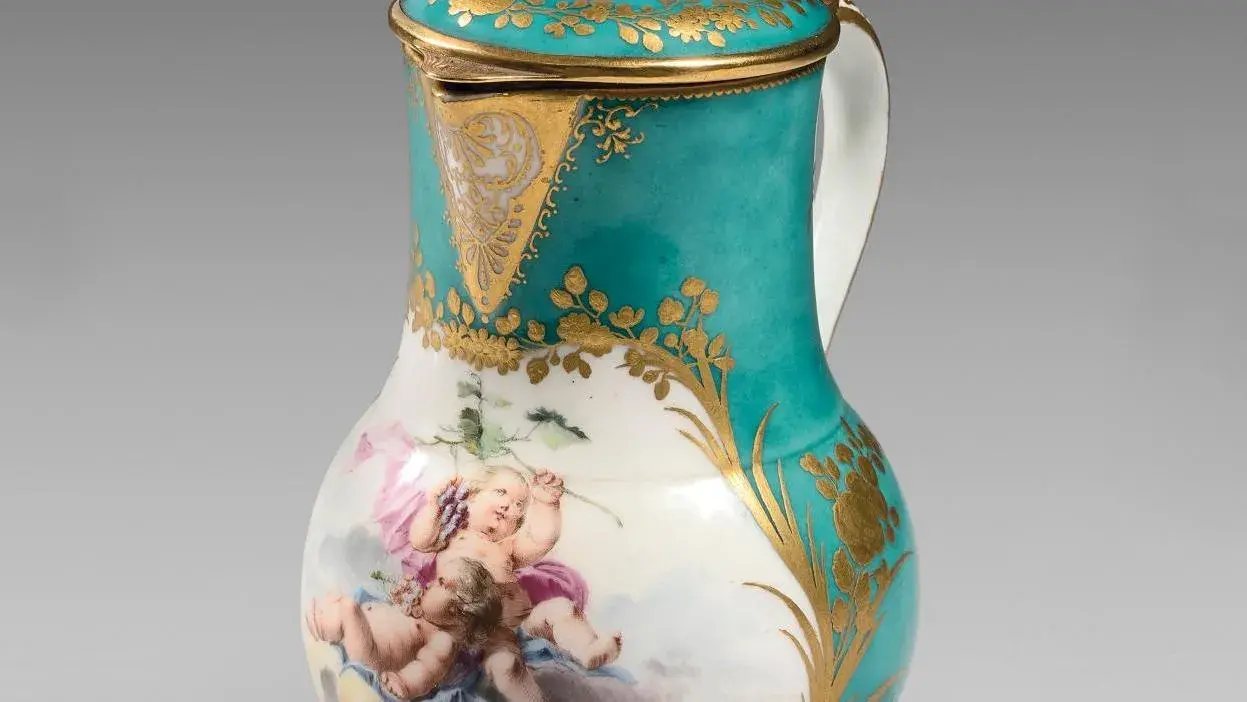
In seeking the secret of Chinese porcelain, France made its mark by creating a remarkable ceramic paste called soft-paste, though it did not contain the vital kaolin. Manufacture de Vincennes, soft-paste porcelain milk jug decorated with two cherubs in clouds eating grapes, after François Boucher (1703-1770), in a reserve of flowers and foliage against a green background, chased gold mounting, date letter for 1754, h. 12 cm/4.7 in. Paris, Hôtel Drouot, January 22, 2021, Beaussant Lefèvre & Associés auction house.Result: €133,350 European admiration for Chinese porcelain led to what soon became a specifically Western product: a ceramic much in vogue for its whiteness and